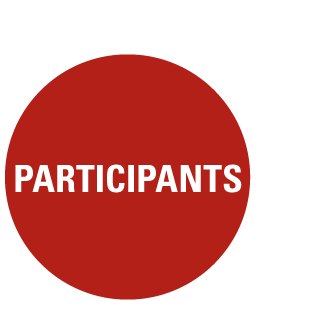
Participant: Selima Akhtar
Country Manager, Bangladesh Impactt
Country Manager, Bangladesh Impactt
Bangladeshi government must be responsible to push up factory inspections, and manufacturers should invest more into making their factories safer. And the more important thing is that U.S and European retailers must demand it and help pay for it. However, behind all these facts, a huge order of clothing in a short time from giant retailers which lead to subcontracting by manufacturer is a major obstacle to improving safety in Bangladesh’s garment industry – the owners of clothing factory in Dhaka revealed.
Vikas Bajaj from The New York Times has the story.
The owner of a clothing factory in Dhaka, Bangladesh, was at New York University last week to meet with clothing industry executives, labor activists and American and European government officials to talk about the Bangladeshi garment industry, the world’s second-biggest exporter of clothes after China.
The workplace disasters in this business have grabbed the world’s attention, and for the past year, Western retailers that outsource their clothing production to Bangladesh have tried to come up with reforms. But there are big obstacles to improving safety in an industry driven by low profits and constant upheaval.
I met with the businessman and another factory owner; both would speak only on the condition that they not be identified because they feared offending their customers. A central problem, the first owner told me, is the rapid turnaround big retailers like Walmart demand when they put in orders for tens of thousands of T-shirts or shorts. Since his factory isn’t able to make all the garments in time, he has to send some of the work to smaller producers. “I can’t do it officially,” he said, “but unofficially, I can.”
Unauthorized subcontracting to smaller, uninspected factories is not supposed to happen, but it remains an entrenched practice. It is a primary reason safety guidelines that apply to bigger contractors have not prevented the hundreds of worker deaths in fires and building collapses in facilities like Rana Plaza, which crumbled last April killing 1,129 people.
The factory owners admitted that what they were doing was wrong. But they said Western clothing companies were also culpable because they often award contracts to manufacturers that they know do not have enough machines and employees to do the job.
Every player has motives to look the other way. The retailers ignore the subcontracting because they would rather manage fewer big contracts, and the per-piece price of garments falls with bigger orders. Suppliers don’t turn down giant orders because they fear they will be shut out of future jobs. “Any vendor in Bangladesh thinks thrice before saying no,” the second owner said to me. And the subcontractors, the lowest on the ladder, are desperate for orders, compete brutally and cannot afford to upgrade their workshops.
H&M is one of biggest contractors of Bangladesh’s clothing factories
Still, the two owners said there are ways to improve the system. Western companies should not award contracts that are so big suppliers cannot realistically fill them without subcontracting. “There should be a switchboard and the red light should go on,” one said. Both pointed to H&M, the Swedish clothing retailer that buys more clothes from Bangladesh than any other Western company, as a model for other firms to follow. They said the company establishes multiyear relationships with factories and keeps track of every subcontractor, including small workshops that might screen-print T-shirts and embroider clothes.
“If customers like H&M didn’t push us,” the second owner said, “we wouldn’t do a lot of things.” Of course, the government needs to step up factory inspections, and Bangladeshi manufacturers should invest more of their profits into making their factories safer. But none of this will happen if clothing retailers in the United States and Europe do not demand it and help pay for it.
The Rana Plaza factory collapse has sought greater commitment from brands across the world especially with regard to auditing procedures in their supply chains. But what exactly is an auditing process, who are its key players, how did it evolve and how can it be made most effective? Rachelle Jackson, Director of Sustainability and Innovation at Arche Advisors, a corporate social responsibility advisory services firm, takes the time to answer these questions in an interview with Boston Global Forum (BGF).
BGF: Tell us a little bit about your organization. What kind of factories does Arche Advisors audit, in which countries and how are these processes carried out?
Rachelle: Arche Advisors is an advisory services firm and we look primarily at issues of corporate social responsibility related to supply chains. That includes labor standards, safety standards and other related issues. Most of our team members have been working in this industry for over ten years. I myself have done more than a thousand audits in about 75 countries over the last 16 years. We started auditing apparel 20 years ago. Apparel auditing was initiated by Levi Strauss who was the first company that conducted supply chain monitoring back in 1989, in response to child labor in Bangladesh. After the apparel sector, many other sectors became aware of these issues in their supply chains so now it’s very common to find giant retail stores like Wal-Mart doing monitoring. Everything you find in a Wal-Mart store, like jewelry, shoes, and electronics, is generally audited. But we’re noticing that more and more food and agriculture farms are getting drawn into this scope for food and beverage companies. We’ve also done work in the extraction sector for coal and gold mines as they have an extended scope of impact on their workers. That is our scope of experience.
BGF: What do you mean when you say ‘auditing’? Do you standardize your auditing processes across different sectors? If so, how?
Rachelle: Great question! It (auditing) has really evolved a lot over time. When social auditing began, back in the mid 1990s, there was a lot of garment production in the US at that time, and the US Department of Labor (DOL) found factories for brands like Guess and Gap to be more like sweatshops. They were constantly finding wage and hour violations and they developed a program where they required these firms to sign a contract with the government. When the DOL found a problem in the factory, they would go to the brand who was purchasing clothes from that factory, and force them to sign a contract with the government which mandated monitoring of labor conditions in those factories on a quarterly basis. Monitoring really developed there through the DOL program. When I started monitoring at a firm, many years ago, we had an ex Department of Labor veteran investigator, and he took the US DOL’s auditing protocol and built a training program for the firm. Hence, private sector auditors were created from this government-monitoring program. We’ve adopted techniques from the US DOL’s inspection program, in order to do what we call ‘social auditing’. The process involves announcing the inspection, arriving at the site, speaking with workers about their working conditions, looking at payroll records and time cards and then walking through the premises to do safety checks. When the work began in the mid 1990s, appearing unannounced at a factory was the norm. Today, most visits are semi-announced which means that a window of time is given to the factory within which the inspection is scheduled to take place. But there is no specific date or time. This change came about because going unannounced gave factories an excuse to prevent auditors from entering- they’d claim that their payroll officer was absent and make other such excuses. With notice, they have to have everything available for the audit or they’ll be challenged for not having that information.
As far as checklists go, audit firms use them as a field tool. Initially companies would let firms dictate how audits should be conducted. But over time, as companies learnt more about social auditing, they would come up with their own protocol, or their own preferred way of conducting an audit. Companies also began to put forward their own checklists. When a company uses more than one auditor, for example Wal-Mart who uses 6-7 audit firms, they give their own protocol and checklists to ensure uniformity. But that comes with its own risks as companies are not always willing to receive feedback from auditors or field people on their protocol. As a result, several experts feel like they may not be receiving the best protocol for auditing, or it’s a lot of paperwork that forces the auditors to spend their time filling out forms instead of talking to the workers. I think it’s very important for companies to be very open to hearing that their approach might not be the best.
BGF: Do you find that companies, especially apparel manufacturing factories, are still insisting on their own methods of protocol or are they more open to feedback?
Rachelle: I think different checklists have begun to merge. Even though there are a lot of different forms and approaches, they all tend to cover the same bases. The concerns don’t lie with checklists themselves. There are other issues that are more concerning, like sample size- how much information does a company require versus how much time they give the auditor to find it out. Reporting formats are another concern- is the reporting template flexible enough that auditors can put in information that needs to be there and is it appropriate in scope and in length for the type of visit that was done. Some companies have really extensive forms and they might have five or six different reports that should be completed from each visit. These tend to be very repetitious and filling them out can take a lot of time away from the audit activity. But checklists are just field tools that auditors use to help write their report. Reports contain all the important information- it allows space for conflicting viewpoints- what the auditors saw versus what the employees said versus the information they got from management and from documentation. As an auditor, we’d want flexibility to report what is important. When forms are too prescriptive then auditors may feel like they lack the flexibility to record valuable observations.
BGF: What happens to auditing reports- do they go to the brands/retailers or subcontractors or to another party?
Rachelle: The reports go to whoever paid for them. There are several different ways these audit activities are funded. A lot of companies, in their social responsibility program, have funding for a certain number of audits. They pay directly to get audits done and they receive the reports. It’s up to them what they do with a report. Some of them will send it to the vendor (or subcontractor) and they may ask the vendor to work with the factory to improve whatever was found in the report. If the company has a smaller supply chain footprint, they may send it straight to the factory instead of a middleman. Normally, the report is used to have a dialogue around next steps and what needs to happen. Audit firms don’t always know how that goes. We may or may not hear back from our clients about improvements made in the factory. At times, they may ask us to go back six months later to do a follow-up audit and we can see for ourselves whether or not the recommendations were taken seriously. In other scenarios, if the middleman has a larger supply chain, the brand company may ask the vendor to bear auditing costs to ensure good social practices at the factories that the vendor has sourced. There are a lot of different ways that these relationships play out.
BGF: How do the recent factory disasters affect auditing procedures? What would you like to see changed?
Rachelle: Various people get blamed after a disaster and what that shows is that it’s a multi-faceted issue. When people say that brands need to do more or audits need to be different or the government needs to focus on enforcement or factory owners need to do more to follow worker safety laws – they’re all right to some degree. Not a single one of them can be successful on their own. Even in the US where we have good enforcement of our labor laws, monitoring began here because the Department of Labor said they were tired of finding problems in factories and they wanted the private sector to have a role.
As far as how the auditing process can be changed, I would like to see companies being less prescriptive in the auditing process. Speaking from example, as consumers when we use financial auditors we don’t tell them how they need to do their audits. We hire them because they are qualified auditors and we trust them to carry out the task following the principles they were trained in. That’s not that way social auditing works although I wish that it were. Auditors and audit firms have made big investments in training, getting field experience and having a professional approach to monitoring procedures but then companies dictate how they should be done. A company should be able to state what they’d like to get out of the audit and what data points they’d like to see but, ultimately, I think that auditors should have the ability to approach their pressures of prescribing to certain checklists and forms. They should go out and be auditors and do the work that they need to do.
Read an interview with Greg Gardener, President and CEO of Arche Advisors, who echoes Jackson’s thoughts on lack of flexibility for auditors and also lends first-hand insight on factory conditions in Bangladesh.
Crisis Advisor at Primark Stores Ltd, Visiting Professor at Dhaka University
Dr Dara O’Rourke has spent the last two decades researching the environmental, social and health impacts of global production systems. His research has evolved to include the study of governmental and non-governmental strategies for monitoring and accountability and new models of public participation in environmental and labor policy. He is currently Associate Professor of Environmental and Labor Policy at the University of California at Berkeley and is the founder of GoodGuide, the world’s largest database on safe, healthy, green, and ethical products based on scientific ratings. Dr O’Rourke has published three books, and several academic articles, including the award-winning Community-Driven Regulation (MIT Press, 2004). His newest book is titled Shopping for Good
In this interview with Boston Global Forum (BGF), Dr O’Rourke discusses loopholes in factory monitoring processes, the role of subcontractors and the development and impact of GoodGuide.
BGF: When did you first realize that labor monitoring in global supply chains was an issue that needed addressing?
Dr O’Rourke: I was doing work in factories in Southeast Asia in the early 1990s but I focused more on environmental issues at that time. I worked for the UNEP in Bangkok and for my PhD dissertation I studied factories in Vietnam, starting in 1994. In 1996, I researched ten factories in Vietnam one of which was producing shoes for Nike. I conducted a waste audit technocratic environmental assessment of the factory’s conditions and found very poor environmental conditions but also discovered very poor work place environment conditions. During my research, Nike had hired Ernst & Young (EY) to audit their factories and, in addition to what we found, EY had documented that two-thirds of the women had respiratory illnesses, massive violations of overtime laws, alleged rapes of women in the factories and other horrendous kinds of physical and verbal abuse.
I spent several months interacting with Nike trying to get them to take these problems seriously but they didn’t. I ended up writing a report on the conditions in these factories which was published in The New York Times in 1997. That is what pulled me from doing technical research to being engaged in broader public debates about work place conditions. I started looking not only into technical issues about air quality within factories and chemicals and toxics used in production but broader labor rights and human rights issues. I’ve done research in the last 15 years inside factories that make global brands of footwear, apparel, toys, electronics, chemicals and processed food and have focused increasingly on interdisciplinary work that looks at the full environmental, social and health impacts of production systems. I moved from technical questions of what chemical or solvent in the shoe causes a respiratory ailment to how you can change systems of governance of these global supply chains to prevent toxics, prevent sweatshops and prevent worker abuse. I conduct research and interact with governments, NGOs, unions and companies on new governance strategies to try and improve conditions in these global supply chains.
BGF: Even with monitoring processes and audits on the ground, why have situations not improved in the last 20 years? What has prevented progressive change from taking place in factories?
Dr O’Rourke: This is the sad part, and it’s mentioned in The New York Times article that we see the same problem surfacing over and over again. It feels like I give the same interview every year or so on the failures of global regulatory systems and the failures of monitoring systems. They continue to not find the problems in these factories or they continue to not solve the problems in these factories.
In the case of Bangladesh and the current global apparel industry, I think they monitor only symptoms of problems in the industry. For example, a checklist audit can observe people working beyond legal limits so they document overtime violations or they document accident and injury rates. The monitoring process is able to identify those symptoms of problems. Our work is to find out how to go from that symptom to a root cause of a problem and answer questions like: why are these accidents occurring and when are they occurring? If they’re occurring between 12am-4am, why are the workers working at that hour? In response, factory managers may say that the order came in late from New York or San Francisco, and they had to work overnight cause the contract said that if they miss the deadline, they would have eat all the material cost and could go bankrupt. By looking deeper, you start going from the accident rate to the overtime to the real cause- which is actually a contract that specifies a delivery time, a speed of operation and a price point that drives the factory to cut costs, work laborers long hours at low pay and eliminate safety procedures. And as you dig further down into the system, I would say the real root cause is the system of fast fashion which consistently drives down prices, speeds up delivery time, increases style changes and puts pressure on the whole system downward, including on the monitoring system where you’ve got a commodity-business of checklist auditing in factories that can’t take the time to progress from symptoms to root causes to solutions for those root causes.
There is a lot of blame to go around in Bangladesh from inspectors to factory managers to corrupt government officials to the parliament itself but there’s a lot of blame in the hands of the US retailers that are specifying, through their contracts, production pricing and delivery times which I think are the root cause of why workers walked back into Rana Plaza on April 24th. Their factory managers knew that if they did not complete those orders, they could go bankrupt. The workers knew that if they did not walk back into the factory, they could lose their job. This is where I think the monitoring systems miss the root cause and focus on symptoms, and at best identify problems. But they’re almost never solve these problems.
BGF: In almost every media report, the subcontractors get blamed from both the demand and the supply end. What’s the role of subcontractors?
Dr O’Rourke: The whole system of global apparel is organized in a fashion such that due to the fast fashion industry, the people who cut the deal are not the same as the people who produce the goods. The deal is cut by big middle organizations, like Li & Fung, but often they are smaller contract or job houses that find factories to produce the goods. What we see repeatedly is that in the day after a catastrophe all the global brands and retailers are scrambling to find out if they have products being produced in those factories. The system is intentionally designed to not only outsource production, but to outsource responsibility for hiring workers, managing the supply chains and dealing with inventory. To meet delivery pressures, the first factory receiving the order illegally subs out some of the order to meet the deadline. The brands have such poor visibility into their own supply chains, that for Rana Plaza, two weeks had passed before Benetton came out and admitted that they had products in Rana Plaza. It was a week after Tazreen (factory fire) that Wal-Mart admitted it had products in Tazreen. These brands intentionally don’t know where their product is being manufactured and they intentionally want to sign a contract with a middleman who is not on the front line.
BGF: So, what’s going to happen to the middleman in the light of these disasters?
Dr O’Rourke: They’re definitely not going to be replaced. None of these brands or retailers want to manage the actual production of their products. They’re going to continue to play a key role and we’ve actually seen an increase in role and an increase in concentration of power and an increasing vertical reintegration among the very large companies. The middlemen are becoming bigger and more powerful and more important. And I would say, that going forward their brands are going to be publicly known. For example, two years ago no one had heard of Foxconn (supplier of electronics) but now Foxconn is a known entity. And the same holds true for Pou Chen (the largest shoe manufacturer in the world) and Li & Fung. I think the middleman will grow in both power and notoriety and their brands will become known brands and they will be targeted by NGOs as key actors in the global supply chain. I don’t see them going away at all; I see them getting stronger.
BGF: How do you source information to rate products according to health, environment and society factors for GoodGuide- your consumer education and information tool?
Dr O’Rourke: We have a science team that conducts ‘product oncology’ which is an assessment using several different scientific methods. We rate our products according to three categories- environment, health and society. For environment, we use life cycle assessments; for health, we use chemical risk assessments and health hazard assessments; and for society we use social impact assessments. Our team looks at a product category and comes up with what matters most on the environmental, health and social impacts across the full life cycle of that product. Our team first identifies what matters most, scientifically, and then develops a complex algorithm with hundreds of attributes, which is passed down to the data team. The data team collects data on those attributes related to the product, the company behind the product and the supply chain. We pull data from different data sources around the world covering six primary areas. These include company self-disclosures, government databases, academic data sources, private research firms, socially responsible investment communities and authoritative NGOs.
The algorithm and data collectively feeds into a process that allows us to rate products and companies on a 10-point scale with 10 being the best. We also have an engineering team that has built our website, iPhone and android apps and a toolbar browser plug-in so consumers can use GoodGuide while shopping on Amazon. We’ve built tools for consumers to help personalize their shopping. The science can be filtered through a consumer’s personal concerns. Example if someone is concerned about animal testing, they can filter out all companies that test their products on animals by using tools on GoodGuide.
The hard work is building the algorithm. Once we’ve built the algorithm, we can rate any company in the world if we can get data on them. It’s a lot of work but it’s designed to be scalable so we can rate any shampoo, any pair of jeans or any cell phone in the world.
BGF: What measurable impact has GoodGuide had?
Dr O’Rourke: We’ve had over 25 million consumers use GoodGuide, a million have downloaded our iPhone app and we have data to show the impact of GoodGuide ratings on consumer purchase and decision-making. On the company side we know from the industries that we’re interacting with, that we’re having a real impact on a number of industries especially in encouraging transparency. We’ve seen a number of industries become much more transparent than they were when we started. And once they become more transparent, we see them phasing out toxic chemicals from their ingredients. But it’s not us alone, we are part of an ecosystem of groups that are moving industries to become more transparent and hopefully phase out some of their worst chemicals and processes.
Controller of Ethical Trade & Sustainability Primark
[For Part 2, please click here]
Boston Global Forum (BGF) had an opportunity to sit down with Professor Kent Jones of Babson College. Dr. Jones specializes in trade policy and institutional issues, particularly those focusing on the World Trade Organization. He has served as a consultant to the National Science Foundation and the International Labor Office and as a research associate at the U.S. International Trade Commission, and was senior economist for trade policy at the U.S. Department of State. Dr. Jones is the author of numerous articles and four books, including Politics vs. Economics in World Steel Trade, Export Restraint and the New Protectionism, Who’s Afraid of the WTO? and most recently, The Doha Blues: Institutional Crisis and Reform in the WTO.
BGF: As an authority on international trade, what do you think will be a possible solution to prevent another Bangladeshi tragedy from happening?
Professor Kent Jones: As any economists would point out, the problem is clear—the building’s standard was extremely poor and, thus, a possible solution must involve the improvement of building standards in factories around the world. However, this is a very complicated task to achieve, and any meaningful procedure must include leadership from multiples fronts—the multinationals, the government, humanitarian groups, NGOs, groups like Boston Global Forum and international organizations such as the ILO [International Labor Organization]. The ILO does have an international labor standard and the ability to send in teams to investigate the safety of factories. However, the problem arises when the ILO does not have enforcement authority, meaning that, even though it can raise concerns over any violations of working standards, the ILO does not have any rights to punish or sanction the respective country. The case for the WTO, however, can be more interesting. As for the idea of having the WTO address this problem, this seems to be attractive to many people, since the WTO does have the authoritative power of pressuring member countries [Bangladesh has been a member since 1995]. The procedure is as follows: if a member nation violates a WTO trade agreement, that country would have to send a representative to present in front of the WTO Dispute Settlement court in Geneva. If the country is found guilty of violating any trade codes, the WTO would allow a certain period of time for the country authority to change its policy. Eventually, if nothing happens, the WTO may then allow the country’s trading partners to raise tariff and/or other fines. Thus, it is an attractive idea that the WTO should play a role in preventing a Bangladeshi tragedy to happen again. Unfortunately, this idea will not work. First, the WTO has a very small budget [195 million Swiss Franc in 2013]. More importantly, the WTO does not protect international labor standard at the moment, and I am skeptical that any discussions to include this issue into the current code would be effective, because every time the WTO adds a certain policy, it has to receive approval from all of its 159 members.
In any cases, our best hope is to have the multinationals at the forefront of this issue, for a number of reasons, but the most important is that these brands all have images they need to keep in the eyes of the consumers. If, for example, Walmart, Macy’s and JCPenney sit down together and develop a “code standard” that requires their subcontractors to maintain the international labor standard, there is possible progress we can rely on.
BGF: You already discussed about the WTO’s role in solving this issue, how about the World Bank and the IMF?
Professor Kent Jones: These two organizations indeed have much larger budgets than the WTO and do have powers to achieve what we hope. The IMF, however, does involve in larger scale projects, for example, improving a country’s financial services sector. The WB, on the other hand, has a lot of potential to be an impactful force on the quest to improve labor standards in the countries which it provides financing.
BGF: Thank you for your time, Professor.
Western multinationals are behind disasters like the Bangladesh factory collapse.
Will public outrage and a new agreement with unions lead to improvements for workers?
On April 24, the Rana Plaza garment fac- tory in Bangladesh collapsed, killing 1,129 workers and injuring at least 1,500 more.
To read full article please download PDF file Kuttner-1.Bangladesh.Aug13
Senior Vice President of Washington Post